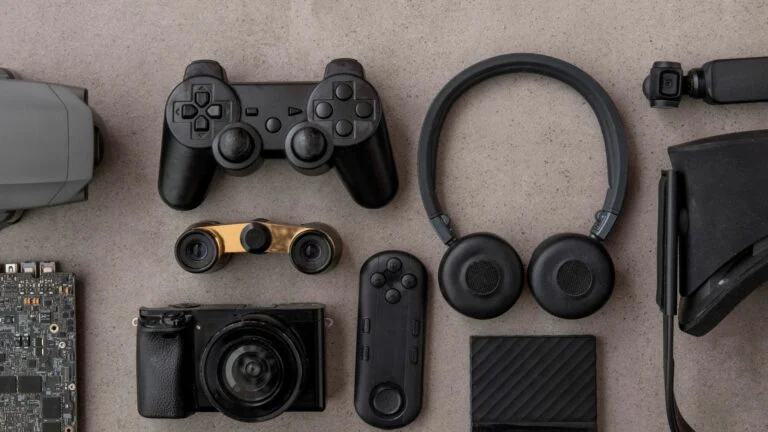
https://baddieshub.co.uk/
The G15 Tool, particularly exemplified by the Figur G15, represents a groundbreaking advancement in sheet metal fabrication. This innovative machine introduces Digital Sheet Forming (DSF) technology, enabling the shaping of sheet metal directly from digital files without the need for traditional tools, molds, or dies. This article delves into the intricacies of the G15 Tool, its technological foundation, historical context, and its transformative impact on various industries.
Understanding Digital Sheet Forming Technology
Digital Sheet Forming (DSF) is a cutting-edge process that allows for the precise shaping of sheet metal through digital instructions. The Figur G15 employs a software-driven ceramic tool mounted on an XY gantry, exerting up to 2,000 pounds of force to mold the metal within a meticulously engineered build zone. This method eliminates the necessity for conventional stamping presses and custom dies, offering a flexible and cost-effective solution for low to medium-volume production runs.
Technical Specifications of the Figur G15
The Figur G15 boasts impressive specifications that cater to a wide range of fabrication needs:
-
Maximum Sheet Size: 1600 mm x 1200 mm (63.0 x 47.2 inches)
-
Forming Area: 1450 mm x 1000 mm (57.1 x 39.4 inches)
-
Z-Axis Travel: 400 mm (15.7 inches)
-
Forming Force: 2000 lbs in X, Y, and Z directions
-
Forming Speed: 1 meter per second
-
Material Capacity: Steel up to 2.0 mm (14 gauge) and aluminum up to 2.5 mm (10 gauge)
-
Power Requirements: 480 V / 3 Phase / 20 kW
-
Machine Dimensions: 2.8 m x 2.2 m x 1.8 m (110.2 x 86.6 x 70.9 inches)
-
Weight: Approximately 8,000 lbs
These features enable the Figur G15 to handle a diverse array of metals and thicknesses, making it a versatile tool in modern fabrication processes.
Historical Context: The Bendix G-15
The term “G15” also harkens back to the Bendix G-15, a computer introduced in 1956 by the Bendix Corporation. Designed by Harry Huskey, the Bendix G-15 was a pioneering machine in the realm of computing, featuring a drum memory of 2,160 29-bit words. Weighing approximately 966 lbs, it was considered one of the first personal computers due to its relatively compact size and accessibility. While technologically distinct from the Figur G15, the Bendix G-15 shares a legacy of innovation and transformation in its respective field.
Applications Across Industries
The versatility of the G15 Tool extends its benefits across multiple industries:
-
Automotive: Facilitates rapid prototyping and production of custom parts without the extensive lead times associated with traditional tooling.
-
Aerospace: Enables the fabrication of complex components with high precision, essential for aerospace applications.
-
Architecture and Construction: Allows for the creation of bespoke metal panels and structures, enhancing architectural aesthetics and functionality.
-
Consumer Products: Supports the development of unique metal products, from household appliances to electronic enclosures, with reduced time and cost.
-
Medical: Offers the capability to produce customized medical devices and equipment tailored to individual patient needs.
-
Industrial Manufacturing: Provides a flexible solution for producing specialized components in low volumes, catering to niche industrial requirements.
Advantages Over Traditional Methods
The G15 Tool’s DSF technology presents several advantages over conventional sheet metal forming techniques:
-
Cost Efficiency: Eliminates the need for expensive stamping presses and custom dies, significantly reducing initial capital investment.
-
Time Savings: By removing the requirement for tool and die production, lead times are drastically shortened, accelerating the manufacturing process.
-
Flexibility: Easily accommodates design changes and customization without the constraints of physical tooling modifications.
-
Precision: Delivers high-quality surface finishes and accurate dimensions directly off the machine, minimizing the need for post-processing.
Implementing the G15 Tool in Modern Manufacturing
Adopting the G15 Tool within a manufacturing setup involves several considerations:
-
Integration: Incorporating the Figure G15 into existing production lines requires an assessment of current workflows and potential adjustments to maximize efficiency.
-
Training: Operators and engineers must be trained to utilize the DSF technology effectively, ensuring optimal performance and safety.
-
Maintenance: Regular maintenance schedules should be established to preserve the machine’s functionality and prolong its operational lifespan.
-
Software Proficiency: Familiarity with the accompanying software is essential for creating accurate toolpaths and achieving desired outcomes.
Future Prospects of Digital Sheet Forming
The evolution of DSF technology, as exemplified by the G15 Tool, indicates a promising future for sheet metal fabrication:
Innovation: Ongoing advancements in materials science, software algorithms, and automation are expected to further enhance the capabilities of Digital Sheet Forming (DSF), making it an even more viable alternative to traditional metal forming techniques.
-
Industry Adoption: As more industries recognize the cost and time benefits of DSF, its adoption rate is likely to grow, leading to an increased demand for machines like the Figur G15.
-
Sustainability: The G15 Tool’s ability to form metal without the waste associated with tooling production aligns with sustainable manufacturing goals, reducing material consumption and energy use.
-
Customization & Mass Customization: With the rise of personalized products and on-demand manufacturing, the ability of the G15 Tool to rapidly create customized components will be a key driver for its adoption across industries.
Frequently Asked Questions About the G15 Tool
What is the G15 Tool used for?
The G15 Tool, specifically the Figur G15, is used for digitally forming sheet metal into complex shapes without requiring traditional stamping dies. It is commonly utilized in industries such as automotive, aerospace, and industrial manufacturing to create prototypes, custom parts, and low-volume production components.
How does the G15 Tool work?
The G15 Tool uses Digital Sheet Forming (DSF) technology, in which a ceramic tool head moves along an XY gantry, applying force to shape the metal according to digital instructions. This process allows for high-precision metal forming without the need for pre-made molds or dies.
What materials can the Figur G15 work with?
The Figur G15 can shape a variety of metals, including steel up to 2.0 mm thick (14 gauge) and aluminum up to 2.5 mm thick (10 gauge). This range allows it to cater to different manufacturing needs while maintaining high precision and quality.
What are the benefits of using the G15 Tool over traditional metal forming methods?
Some key benefits include cost savings (by eliminating expensive dies and tooling), faster production cycles (since no tooling needs to be made), greater design flexibility, and the ability to manufacture customized or low-volume parts efficiently.
How does the G15 Tool impact the future of sheet metal fabrication?
The G15 Tool represents a shift toward more flexible and sustainable manufacturing processes. Its digital approach to metal forming allows for more efficient production, less material waste, and the ability to produce highly customized components quickly. As DSF technology evolves, it is expected to become a standard method for certain types of sheet metal fabrication.
Is the Figur G15 Tool suitable for mass production?
While the Figur G15 excels at low to medium-volume production, its DSF technology is not designed to replace high-speed mass production methods such as stamping presses. However, it is ideal for custom manufacturing, prototyping, and industries where flexibility and rapid iteration are more valuable than sheer production speed.
Conclusion
The G15 Tool, particularly the Figure G15, is revolutionizing the world of sheet metal fabrication through Digital Sheet Forming (DSF). By eliminating the need for traditional dies and tooling, it offers manufacturers a faster, more cost-effective, and more flexible way to create complex metal parts. From automotive to aerospace and beyond, industries are recognizing the potential of this groundbreaking technology to reshape how metal components are designed and manufactured.
As DSF technology continues to advance, the G15 Tool is poised to become an integral part of modern manufacturing, bridging the gap between digital design and physical production. Whether used for rapid prototyping, customized manufacturing, or innovative design applications, the G15 Tool is setting new standards in precision, efficiency, and sustainability.
With its remarkable capabilities and future potential, the Figure G15 is not just a tool—it’s a glimpse into the next era of digital manufacturing.
1 thought on “The G15 Tool: Revolutionizing Sheet Metal Fabrication”